Concrete Floor Paint
Are you looking to paint a concrete or cement floor? As industrial floor paint manufacturers, we continually make a range of the best concrete floor paints for you to choose from.
Designed to protect the substrate and enhance the appearance of the floor, choosing a suitable coating for concrete surfaces is vital.
By choosing the right type of paint and properly preparing and maintaining the surface, concrete floors can be transformed into durable, attractive, and long-lasting surfaces.
Our range includes polyurethane, anti slip, quick drying, and epoxy floor paints.
Do you need help or technical advice?
It can be difficult to choose if you are not familiar with the technical aspects of the products. If you need any help, we do have informative blog posts available in the help and advice section of the website. We are also always happy to provide all the assistance you need over the phone, so please don’t hesitate to call us on 01782 550733.
Anti Slip Quick Dry Concrete Floor Paint is a made with the addition of a wax additive to give more slip resistance to your floor. This is a single pack paint (does not need an activator) and gives protection against solvent, salt and water damage. Having good durability and impact resistance, it is suitable for use in heavy duty commercial and industrial areas. – Coverage: 5-10 m² per litre – Touch Drying Time: 3-6 hours – Recoat: 24 hours – Hard Drying Time: 48 hours
Two Pack High Build Epoxy Garage Floor Paint - Designed for application to concrete, cement and non ferrous metals. Excellent resistance to water, solvents, acids, alkalis and salts. Gives superb adhesion to all recommended substrates. Tough finish has long lasting abrasion and impact resistance. Recommended for areas receiving heavy traffic (vehicle / trucks). - Coverage: 5-7 m² per litre - Touch Drying Time: 12-16 hrs - Recoat: 24 hrs - Hard Drying Time: 48 hrs - Full Cure: 7 days
Polyurethane Concrete Floor Paint - A single pack high build floor coating giving medium durability against abrasion and impact, with limited protection against solvent, salt and water damage. Polyurethane Concrete Floor Paint is easy to apply with a gloss or semi-gloss finish. Suitable for light commercial and industrial areas.
Quick Dry High Build Floor Paint - A single pack quick dry floor coating which provides good durability against abrasion and impact along with with protection against solvent, salt and water damage. Very easy to apply. Suitable for heavy duty commercial and industrial areas.
Two Pack Epoxy Floor Paint (Top Coat) - This epoxy floor coating is designed for application to concrete, cement and non ferrous metals. It provides excellent resistance to water, solvents, acids, alkalis and salts and gives superb adhesion to all recommended substrates. Tough finish has long lasting abrasion and impact resistance. Recommended for areas receiving heavy traffic (vehicle/trucks). Following application of the product: Do not park vehicles or place heavy equipment on the floor for a minimum of 48 hours Do not get the floor wet for a minimum of 7 days as this will cause bloom (discolouration) - Coverage: 5-7 m² per litre - Touch Drying Time: 12-16 hrs - Recoat: 24 hrs - Hard Drying Time:48 hrs - Full Cure: 7 days
Two-Pack Epoxy Floor Sealer (Under Coat) - This epoxy floor paint (first coat) is designed to prepare the surface of concrete, cement and non ferrous metals. This gives an ideal base for epoxy topcoat or acts as a seal coat for bare concrete floors. Resistant to water, solvents, acids, alkalis and salts. Tough finish, and has long lasting abrasion and impact resistance. Recommended for areas receiving heavy traffic (vehicle/trucks). Following application of the product: Do not park vehicles or place heavy equipment on the floor for a minimum of 48 hours Do not get the floor wet for a minimum of 7 days as this will cause bloom (discolouration) - Coverage: 5-7 m² per litre - Touch Drying Time: 12-16 hrs - Recoat: 24 hrs - Hard Drying Time: 48 hrs - Full Cure: 7 days
Floor Primer made to use in conjunction with any of the Regal single pack topcoat floor paints. Not suitable for use with our epoxy topcoat floor paint. Regal Prime and Seal is a single pack, quick drying, low viscosity, penetrating first-coat floor primer. Designed to soak into the substrate, it enhances adhesion of subsequent top coats by acting as an anchor layer between the substrate and floor paint. Regal Prime and Seal dries with a flat finish. The colour is non specific. - Coverage: 5-10 m² per litre - Touch Drying Time: 2-4 hours - Recoat: 24 hours - Hard Drying Time: 24 hours You might be thinking does floor paint need primer? Please read our information page 'what does floor primer do?'.
SuperTough Aggregate is an iron-silicate grit. With much larger particles than our Pumice Aggregate, it has a hard, sharp finish to give fantastic grip when used in conjunction with our floor paints. To use SuperTough Aggregate, firstly apply a coat of floor paint and then liberally scatter the grit over the surface of the wet paint. Allow the floor to dry for a full 24 hours. Once dry, use a soft brush to remove the excess SuperTough Aggregate that hasn’t stuck. Then paint over the whole surface of the floor again to seal the grit in place on the floor.
Single Pack Concrete Paint - Overview
Our single pack range of floor paints include our ever popular durable and slip resistant “Antislip Quick Dry Concrete Floor Paint”. This concrete paint is a godsend for jobs where the floor is used in an environment that might become damp and represent a hazard to visitors such as commercial and industrial areas. These heavy duty paints also offer a degree of chemical resistance and 24 hour drying times. If you prefer a floor paint with a more glossy finish and don’t require the same levels of protection against solvents, salt and water, our Polyurethane Concrete Paint may be a slightly cheaper and more suitable choice. Those looking for a paint that provides a very thick covering, perhaps in heavy traffic areas where they are trying to create a heard wearing, smooth surface, our “Quick Dry High Build Floor Paint” is a great choice.Two Pack Concrete Paint - Overview
In addition, Regal are specialists in the manufacture of two pack paints. These epoxy floor paints are especially suitable for application as a garage floor paints as they have excellent chemical resistance, a tough, impact resistant finish and will stand up to heavy traffic from vehicles and trucks. Epoxy floor paint come in two parts and in two stages. The first stage is to mix and apply the two pack epoxy floor sealer, as this provides the right base for the top coat as part of the two pack floor coating system. The product is delivered, as the name suggests, in two packs. Mixing them together in the proportions they are provided in initiates the chemical reaction that leads to a hard wearing epoxy finish that is superior to those achievable by single pack paint solutions. In order to use, take its activator and paint and ensure gentle but thoroughly mixing using a paint mixer tool. A range of brushes and tools are available for the purpose of ensuring a pleasing application of paint and we would be happy to discuss your requirements with you and advise on available options. Upon coating, care must be taken to avoid getting the floor wet for 7 full days as this leads to discolouration called “amine blush” or “amine bloom”. Once fully dry, this first coat can be painted with two-pack top coat. Provided a full 48 hours are allowed during which no heavy vehicles or equipment are placed on the floor, you will end up with a painted surface that will look great for many years!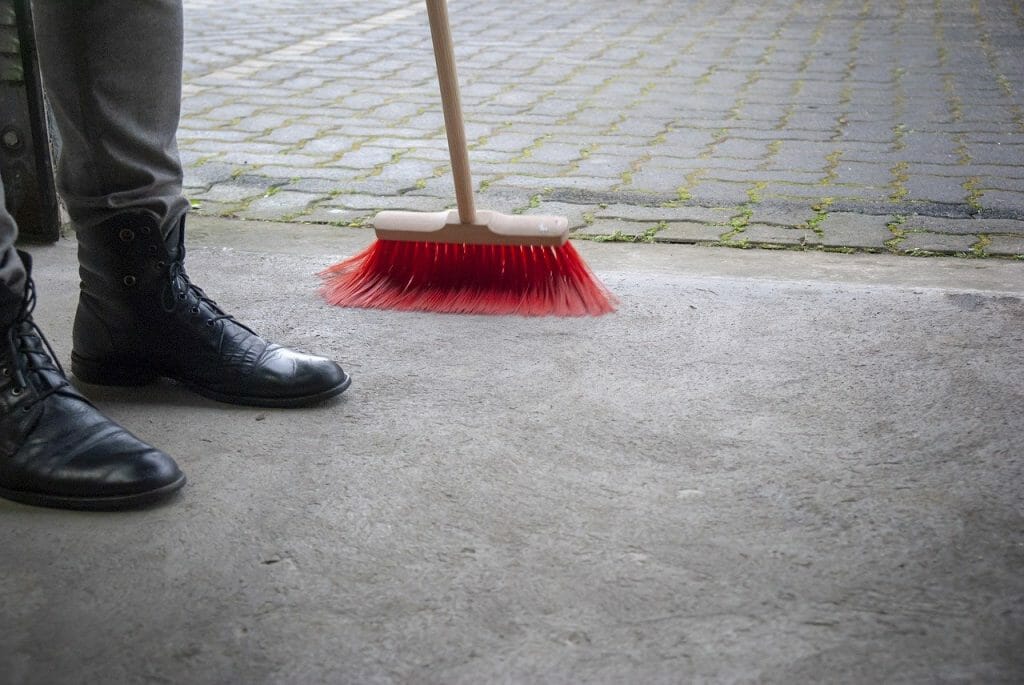
"Surface preparation is time well spent on concrete even more than any other substrate."
So Which Concrete Paint is Right for Me?
Painting concrete comes with it’s own set of challenges compared to the painting most of us are used to. Concrete can have varying degrees of humidity, alkaline bloom (sometimes called surface laitance especially on new concrete where the lime in the mix has floated to the surface), oil and grease contamination on older floors not to mention the porosity can mean that water from below can by pushed up through the concrete by hydraulic pressure when the water table rises. Older concrete can also be contaminated with algae or other forms of biological growth hence the term often found when talking about old concrete referred to as “green” concrete. All of these challenges can be overcome with a little careful planning and good surface preparation and choice of the right product for the job. This is a job for specially formulated Concrete Floor Paint.Preparation is Key
Concrete Paint requires good surface preparation prior to use for the best results followed by the right product from the range of Concrete Floor Paints available for your needs. To get a good result the surface should be cleaned down well using clean and degrease and allowed to dry thoroughly. Surface preparation is time well spent on concrete even more than any other substrate.The "Right" Paint Choice Depends on the Floor Use
Having cleaned and dried your concrete floor it requires some careful thought as to the intended use of concrete floor once the floor has been painted. Tackling the key reasons why the floor needed to be painted determines the best Concrete Floor Paint to use. These include suppressing the dust, covering up tyre or paint or oil spillage marks, wanting to improve the anti-slip properties of the concrete as (particularly with power floated concrete) the original concrete is slippery when wet after the car has been garaged after being out in the rain. It could even be that if space is tight you feel painting the space on the floor, your own “parking bay” makes it easier to make the best use of the garage or allocated parking and of course sometimes for aesthetic reasons you want to paint over the old micro cracks and discolouration on the floor by using suitable concrete garage floor paint.Some Advice on Using Single Pack Paint
For most consumers, a light duty Concrete Floor Paint used by modern paint producers formulated as a single pack product based on resins derived from renewable resources are favoured. These “modified alkyd” resins can include a higher than normal anhydride content or chain stopping agent to reduce mechanical damage (scratching) and blocking (also known as pick up for dirt). Polyurethane modification is also possible to improve toughness and the use of solvents with lower odour (so called dearomatized solvents) and these are also popular as Concrete Floor Paints for large light duty warehouses which have to be back in operation quickly – sometimes in as little as a single shift since they are easy to apply, have no pot life and can be applied by the workers without employing specialist labour using a brush or roller. Spray painting is possible but usually this is not used as the wastage factor is higher than by roller (by around 20%) which for large areas can be significant. Concrete Paint also has advantages in high use areas where touch in repainting saves repeating the whole job since they have few overcoating or repainting issues. This also makes them ideal for consumer use and they are available as a quick drying or standard type depending on the time available to first use. However, it is good practice to allow a newly painted concrete floors to dry through thoroughly for a few days before driving on it with rubber tyres (the twisting action of turning the wheels to change direction can act like a suction cup and pull away patches of paint where the tyre was standing). This is often caused by solvent trapped under the dry surface of the Concrete Paint which can take little longer to disappear even from an apparently dry hard surface. For this reason two thin coats give a better end result than a single thick coat with these modified alkyd types, the first coat to prime and seal the concrete and the second coat to give the finish. This is particularly true if the paint has been allowed to “pool” and become thicker than the rest, for example where a small indentation in the concrete has allowed the paint to “settle”.Concrete Paint Formulation
Concrete Floor Paint is carefully formulated to carry out specific functions. Concrete floors, usually contains lime as part of the mix. Concrete Floor Paint is formulated to avoid saponification (alkali hydrolysis) particularly on new or untreated concrete where the white lime (surface laitance) can be clearly seen where the lime has floated to the top removing this surface laitance greatly improves the life of the coating and whilst professionals usually do this with a mild acid etc for consumer use this is not always practical so a good cleaning with clean and degrease can go a long way to improving the results. Concrete Floor Paint also has to have good wear resistance and flow so that brush and roller marks disappear but also to allow the wear resistance to develop and on anti skid coatings the additives to “bind” into the coating. This is why it is always a good idea to follow the manufacturers recommendations especially concerning preparation and priming the concrete.When to Use Two-Pack Epoxy
Concrete Floor Paints based as mentioned previously on “modified alkyd” technology from renewable plant raw materials are good general purpose products. However, heavy duty use or longer maintenance cycles require a thermoset resin technology. The best thermoset resin for Concrete Floor Paint uses epoxy resin. Solvent or solvent free Epoxy Floor Paints are not as easy to use and overcoat as their single pack brothers but offer longer life, improved chemical and wear resistance. They are also more expensive, comprise 2 or sometimes 3 components which must be mixed prior to use and can’t be used once the pot life is over. This means that for people working alone doing a domestic type concrete floor you have to finish the job in a few hours or carefully weight out of each component only as much as you can use in the pot life. This can be an extra complication which many consumers don’t feel comfortable with whereas with an alkyd, you can stop at any time, reseal the tin and finish it later – perhaps after lunch? Overcoating is also more difficult with Epoxy Resin Floor Paint as it is formulated to resist abrasion so sanding previous coats to improve adhesion can take time without specialist mechanical sanders for floors. These are available and can be hired but most consumers prefer a simpler solution and just to repaint every 2 – 3 years or the ability to patch in marks and damage easily.In Summary
To summarise, Concrete Floor Paint gives good results but choice of technology is dependent on what use you will put the floor too. Concrete Paint can give a good professional result even in the hands of novice with a little attention to surface preparation and choice of Floor Paint. You should always follow the manufacturers application instructions.Regal Paint® - Floor Paint Manufacturers
Regal Paint® manufactures hard wearing, long lasting, high-performance floor paint for a complete range of applications, both industrial and commercial. Our floor paints are ideally suited for application on warehouse floors, factory floors, commercial garages, MOT centres, showrooms, chemical plants, galleries and much more. Regal Paints are specialist manufacturers of epoxy floor paint, concrete floor paint, quick-drying paint, garage floor paint and more. Please contact us to discuss your requirements or consult our floor coatings FAQ section for more information..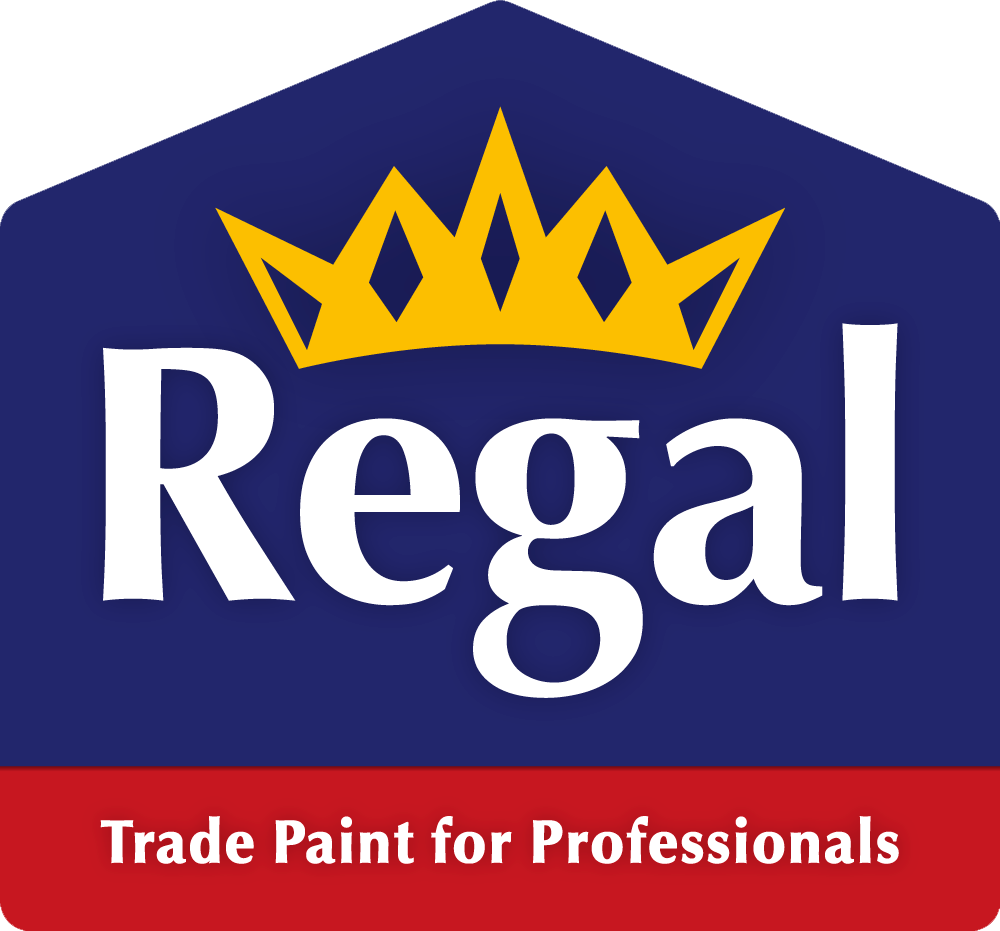